倉庫の棚卸しで重要な点とは?作業法や改善方法を紹介
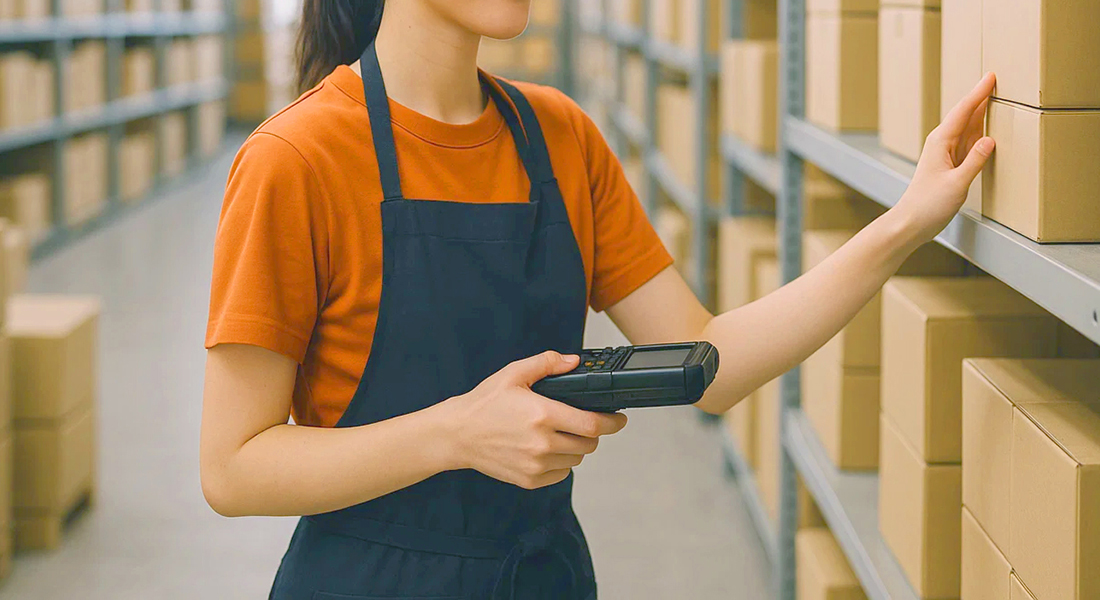
棚卸しの重要性
棚卸しは、物流倉庫運営において必須のプロセスであり、正確な在庫管理とビジネスの健全性維持に寄与します。
棚卸しの目的とその必要性
棚卸しの主な目的は、倉庫内の物理的な在庫と帳簿上の記録が一致していることを確認することです。このプロセスは、商品の過剰在庫や不足を明らかにし、倉庫の空間を効率的に活用するための重要な情報を提供します。例えば、日本のある物流倉庫では、定期的な棚卸しにより年間の商品ロスを5%削減し、その結果、経営効率が大幅に改善されました。棚卸しは、不正確な在庫データによる誤った発注のリスクを減らし、必要な在庫レベルの維持を支援するために必要です。
棚卸しのビジネスへの影響
棚卸しはビジネス運営に大きな影響を及ぼします。正確な棚卸しデータは、需給計画の正確性を向上させ、顧客満足度の向上に寄与します。また、棚卸しによって特定された過剰在庫は、キャッシュフローに悪影響を及ぼす可能性があり、その管理は企業財務に直接影響します。日本の倉庫運営会社では、棚卸しを通じて在庫の正確性を98%以上に保つことで、顧客への迅速な配送を実現し、年間で顧客満足度を20%向上させる成果を達成しています。また、棚卸しは不良在庫の早期発見にも役立ち、製品の品質管理を強化します。
棚卸しの計画と準備
物流倉庫における棚卸しのプロセスは、在庫の正確性を保証し、経営の効率化を図る上で欠かせない要素です。効果的な棚卸しを行うためには、事前の計画と準備が重要となります。
棚卸し計画の作成
棚卸し計画の作成には、倉庫内の在庫アイテムの全リストアップが必要です。これには、倉庫の各区画ごとにどの商品がどれだけ保管されているかの詳細な記録が含まれます。例えば、日本の中規模物流倉庫では、棚卸しを年に2回計画しており、そのたびに商品カテゴリーごとに在庫数の目標と現実との差異を確認し、95%以上の在庫正確性を維持しています。棚卸し計画は、予期せぬ過剰在庫や不足を防ぐためにも重要です。
必要なリソースとツールの準備
棚卸しに必要なリソースとツールの準備も、計画的に行う必要があります。これには、棚卸しに使用するバーコードスキャナーやタブレット、棚卸し作業用の専用ソフトウェア、必要な場合は追加の人員の手配などが含まれます。効率的な棚卸しを実現するためには、最新の技術を活用することが推奨されます。たとえば、RFID技術を用いることで、手作業による入力ミスを減らし、作業のスピードを大幅に向上させることが可能です。
従業員への事前トレーニング
棚卸し作業の効率を最大化するためには、従業員への事前トレーニングが不可欠です。トレーニングでは、使用するツールの操作方法や棚卸しの手順、注意点などを徹底して指導します。日本のある物流倉庫では、棚卸し前に全従業員を対象にしたトレーニングセッションを実施し、棚卸し作業の正確性を向上させるとともに、作業効率を20%改善した例が報告されています。適切なトレーニングにより、棚卸し作業のミスを減らし、在庫管理の正確性を保つことができます。
効率的な棚卸し作業法
効率的な棚卸し作業は、倉庫の在庫管理を最適化し、物流プロセスの効率を高めるために不可欠です。ここでは、物理的な棚卸しとデジタル棚卸しの方法、ピッキングリストの使用、バーコードシステムとRFIDの活用について説明します。
物理的な棚卸しとデジタル棚卸しの方法
物理的な棚卸しは、従業員が倉庫内の商品を直接確認し、数量を手動で記録する伝統的な方法です。一方、デジタル棚卸しでは、バーコードスキャナーやRFIDリーダーを使用して商品情報をデジタルで読み取り、在庫管理システムに直接入力します。日本のある倉庫では、デジタル棚卸しを導入することで棚卸し作業の時間を従来の半分以下に短縮し、在庫の正確性を99%以上に向上させることができました。
ピッキングリストの使用
ピッキングリストを使用することで、棚卸し作業をより効率的に行うことができます。ピッキングリストは、倉庫内の商品の正確な位置と数量を示す書類で、従業員が迅速に商品を特定し、在庫を確認するのに役立ちます。
バーコードシステムとRFIDの活用
バーコードシステムとRFID技術の活用は、効率的な棚卸し作業において非常に有効です。バーコードやRFIDタグを商品に付けることで、商品情報を瞬時に読み取り、在庫管理システムに自動的に入力することが可能になります。日本の大手物流倉庫では、RFID技術を導入したことで、従来のバーコードスキャンに比べて棚卸し作業時間を30%削減し、在庫の追跡と管理の正確性を大幅に向上させています。
ヒューマンエラーの軽減
倉庫内の棚卸し作業では、ヒューマンエラーの軽減が重要な課題です。正確な在庫管理を実現するために、エラーを最小限に抑える方法とその対処法について検討します。
チェックリストの利用
チェックリストの利用は、倉庫での棚卸し作業におけるヒューマンエラーを減らす効果的な手段です。棚卸し作業前に具体的な作業手順や確認項目をリスト化し、作業者がそれに従って作業を進めることで、作業の漏れや間違いを防ぎます。日本のある倉庫では、チェックリストを使用することで、棚卸し時のエラーレートを従来比で約30%削減したと報告されています。この方法は、特に新しい従業員やアルバイトスタッフが多くを占める倉庫で有効です。
二重チェックシステム
二重チェックシステムの導入も、倉庫での棚卸し作業におけるヒューマンエラーを軽減する有効な策です。このシステムでは、最初に作業を行ったスタッフとは別のスタッフが、作業結果を再確認します。このプロセスを通じて、初回のチェックで見落とされたエラーや不備を発見し、修正することができます。日本の中規模倉庫で実施したケーススタディでは、二重チェックシステムを導入することで、棚卸しの精度が95%以上に向上したとの結果が得られました。
エラー発生時の対処法
ヒューマンエラーが発生した際の迅速な対処法も、倉庫での棚卸し作業の効率化に不可欠です。エラーを発見した場合は、直ちにその原因を究明し、同様のエラーが再発しないように対策を講じます。例えば、エラーの原因が不明確な指示にある場合は、作業指示書の見直しや従業員への追加トレーニングを行います。また、日本のある大手倉庫では、エラー発生時にはその都度フィードバックを従業員に提供し、継続的な改善活動を行うことで、エラーレートを年間で20%削減することに成功しました。
棚卸しデータの分析と活用
倉庫での棚卸しは単なる在庫確認作業にとどまらず、収集されたデータの分析と活用によって、効率的な在庫管理とビジネス戦略の最適化が可能になります。
データの正確な記録と分析
倉庫内での棚卸し作業においては、在庫データの正確な記録が非常に重要です。この記録されたデータを分析することで、在庫管理の精度を高めることができます。例えば、特定の商品が予想以上に早く売れていることが分析で判明すれば、その商品の発注量を増やすことで売り上げ機会の損失を防ぐことが可能です。また、データ分析を通じて、倉庫内の商品配置を最適化し、ピッキングの効率を上げることも可能になります。
在庫の過剰や不足の特定
棚卸しデータの分析を通じて、在庫の過剰や不足を特定することができます。過剰在庫が発見されれば、それに応じてプロモーション活動を計画することで在庫を効率的に減らすことができます。また、特定の商品の在庫が常に不足している場合は、供給元との契約見直しや代替商品の検討など、対策を講じることが必要です。在庫の過剰や不足は、資金の無駄遣いや顧客満足度の低下に直結するため、早期の特定と対策が求められます。
未来の在庫管理へのフィードバック
棚卸しで得られたデータとその分析結果は、未来の在庫管理戦略を形成するための貴重なフィードバックとなります。過去のデータから季節性の変動や市場の動向を読み解き、それを未来の在庫計画に反映させることで、より精度の高い在庫管理が可能になります。たとえば、年末年始やゴールデンウィークなどの特定の時期に需要が増加する商品については、事前に在庫を確保することで、売り上げ機会の最大化を図ることができます。
棚卸し作業の改善方法
倉庫内の棚卸し作業は、在庫の正確性を保証し、効率的な倉庫管理を実現するために不可欠です。以下では、棚卸し作業の改善方法について具体的な手法を紹介します。
プロセスの自動化とシステム化
倉庫での棚卸し作業を効率化するためには、プロセスの自動化とシステム化が鍵となります。例えば、バーコードやRFIDタグを用いた在庫管理システムを導入することで、在庫の記録と追跡を自動化し、手作業によるエラーを大幅に減少させることができます。実際に、日本のある倉庫では、自動化システムの導入により棚卸し作業の時間を以前の半分以下に短縮し、在庫の正確性も大幅に向上したと報告されています。
定期的なサイクルカウントの実施
全在庫を一度に数える代わりに、定期的なサイクルカウントを実施することで、棚卸し作業の負担を軽減し、在庫の正確性を維持することができます。サイクルカウントでは、倉庫内の在庫を部分的に順番に数えていき、年間を通じて全在庫のチェックを行います。この方法により、特に在庫の動きが早い商品や高価値商品の在庫管理を強化できます。日本の複数の倉庫で実践されており、継続的な在庫精度の向上に貢献しています。
棚卸し後のレビューと改善計画
棚卸し作業後には、その結果を詳細にレビューし、見つかった問題点に対する改善計画を立てることが重要です。棚卸しで発見された過剰在庫や不足在庫の原因を分析し、その原因を取り除くための具体的なアクションプランを策定します。例えば、不足在庫が多い場合は、発注プロセスの見直しや、サプライヤーとのコミュニケーション強化が必要になるかもしれません。日本のある企業では、このようなアプローチにより、次回の棚卸しでのエラー率を顕著に減少させることに成功しました。
適切な倉庫管理システムの導入
倉庫内での効率的な棚卸し作業は、適切な倉庫管理システム(WMS)の導入によって大きく向上します。これにより、正確な在庫情報の維持、作業効率の向上、ヒューマンエラーの削減が可能になります。
倉庫管理システム(WMS)の利点
倉庫管理システム(WMS)の利点は、倉庫運営の各側面においてその価値を倍増させます。まず、在庫管理の正確性を格段に向上させることで、過剰在庫や品切れのリスクを効果的に低減します。これにより、資金の無駄遣いを防ぎつつ、顧客への確実な供給を実現できるようになります。また、WMSは入出庫作業を自動化し、手作業によるエラーを削減することで、オペレーションの速度と精度を同時に高めます。これは、特に注文処理時間の短縮と緊急の顧客要求に迅速に対応する能力の向上に寄与します。
さらに、WMSによるリアルタイムの在庫データの提供は、棚卸し作業の効率化だけでなく、より戦略的な在庫管理への道を開きます。倉庫スタッフは、最新のデータに基づいてより精密な在庫調整を行うことができ、これが倉庫のスペースの最適化と運営コストのさらなる削減に繋がります。加えて、WMSは詳細なデータ分析機能を備えており、消費者の購買傾向や季節的な需要変動など、様々なインサイトを提供します。これにより、企業はより効果的な在庫戦略を立てることができ、長期的なビジネス成長をサポートします。
最終的に、WMSの導入は倉庫運営の透明性を高め、顧客サービスの質を向上させることに寄与します。正確な在庫情報と効率的な作業プロセスは、顧客からの信頼を勝ち取り、リピートビジネスに繋がります。このようにして、WMSは単なるコスト削減のツールではなく、顧客満足度と企業の競争力を向上させるための戦略的資産としての役割を果たします。
システム選定のポイント
倉庫管理システムを選定する際には、いくつかのポイントを考慮する必要があります。まず、自社の倉庫運営の規模とニーズに合った機能を持つシステムを選ぶことが重要です。また、システムが提供するデータの可視化機能やレポート機能が、棚卸し作業や在庫管理の改善に役立つかどうかを検討する必要があります。さらに、ユーザーフレンドリーな操作性やサポート体制も、長期的な運用を考える上で重要な選定基準となります。システム導入の前には、実際の運用シナリオを想定したデモンストレーションを受け、その効果を確認することが推奨されます。
まとめ
適切な倉庫管理システムの導入は、倉庫内での棚卸し作業を含む日常運営を効率化し、正確な在庫管理を実現するために不可欠です。システム選定時には、自社の具体的なニーズに合った機能、操作性、サポート体制を備えたものを選ぶことが重要です。これにより、棚卸し作業の効率化、在庫の正確性の向上、コスト削減、顧客満足度の向上といった多岐にわたるメリットを享受することが可能となります。