倉庫の無駄コストを削ぎ落とす|効率的な在庫管理でヒューマンエラーを無くす倉庫の改善法
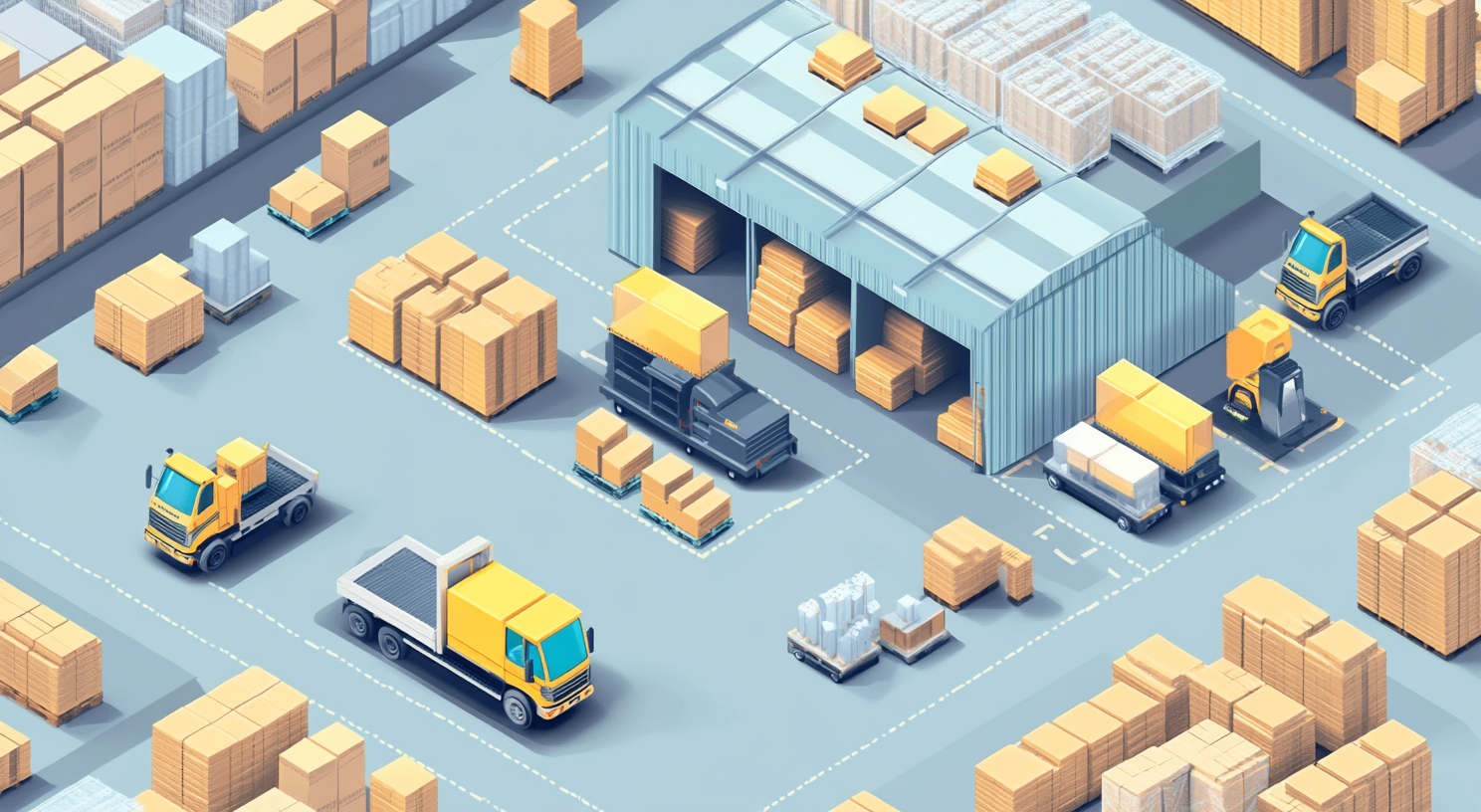
倉庫運営における無駄コストの特定
始めの重要なステップです。特に「倉庫」と「在庫管理」に関わる活動を見直すことで、運営の最適化を図り、全体的な物流コストの削減に繋がります。
無駄コストの一般的な原因
倉庫運営における無駄コストの一般的な原因には、非効率な在庫管理、過剰な安全在庫の保持、物品の配置ミス、出入荷作業の非効率などがあります。これらは「倉庫」のスペースを無駄に使用し、「在庫管理」の精度を下げる要因となり、結果的にコスト増加に繋がります。また、倉庫内の作業手順が最適化されていない場合、従業員の作業効率が低下し、余分な人件費が発生する可能性もあります。これらの問題を洗い出し、改善策を講じることが倉庫運営の効率化には不可欠です。
在庫過剰と不足、保管スペースの無効活用
在庫管理における最大の課題は、在庫過剰と不足のバランスを如何に取るかです。在庫過剰は「倉庫」の保管スペースを不必要に占有し、資金の流動性を低下させます。一方で、在庫不足は顧客満足度の低下や機会損失を引き起こす可能性があります。また、保管スペースの無効活用は、倉庫の有効スペースを圧迫し、新たな在庫を受け入れる能力を低下させます。これらの問題に対処するためには、正確な需要予測と効果的な在庫回転率の管理が求められます。適切な「在庫管理」システムを導入し、定期的な在庫見直しを行うことで、無駄コストの削減と倉庫運営の最適化を図ることが可能です。
効率的な在庫管理の基本
効率的な在庫管理は、「倉庫」運営の成功に不可欠な要素であり、コスト削減、顧客満足度の向上、そして業務効率化に直接貢献します。「在庫管理」の基本を理解し、適切に実践することで、倉庫内の運営を大きく改善できます。
適正な在庫レベルの維持
適正な在庫レベルを維持することは、「倉庫」のスペースを最大限に活用し、「在庫管理」の効率を高めるために非常に重要です。過剰な在庫は資本の無駄遣いであり、不足は顧客の要求を満たせないリスクを生み出します。効率的な在庫管理システムを導入することで、需要の変動に応じて在庫レベルを自動調整し、適正な在庫量を保つことが可能になります。このプロセスには、過去の販売データの分析や、季節性、市場のトレンドなどを考慮した需要予測が含まれます。
在庫の見える化とリアルタイム管理
「在庫の見える化」は、「倉庫」での効率的な「在庫管理」のために不可欠です。在庫の正確な情報をリアルタイムで把握することにより、倉庫内の在庫状況を常に最適な状態に保つことができます。在庫の見える化を実現するためには、バーコードシステムやRFIDタグなどのテクノロジーを利用し、入出荷の追跡、在庫の場所、数量、状態などの情報をリアルタイムで管理するシステムの導入が効果的です。これにより、在庫過剰や欠品のリスクを大幅に減らし、迅速な出荷対応が可能となり、結果的に顧客満足度の向上に繋がります。
在庫管理システム(WMS)の活用
在庫管理システム(Warehouse Management System、WMS)の活用は、「倉庫」運営と「在庫管理」の効率化を大幅に改善する重要な戦略です。このシステムを適切に利用することで、倉庫内の作業プロセスを最適化し、在庫の正確性を高めることができます。
WMSの概要とメリット
WMSは、倉庫内の在庫の受け入れ、保管、出荷プロセスを管理するためのソフトウェアシステムです。このシステムの最大のメリットは、在庫の正確な追跡と管理を実現することで、「倉庫」のスペース利用を最適化し、「在庫管理」の精度を大幅に向上させることができる点にあります。また、WMSはリアルタイムでの在庫情報の更新を可能にし、在庫過剰や欠品のリスクを最小限に抑えることができます。さらに、注文処理の自動化により、出荷ミスの減少と顧客満足度の向上にも貢献します。
カスタマイズ性の高いWMSを導入してミスの起こらない環境を
カスタマイズ性の高いWMS(Warehouse Management System)を導入することは、「倉庫」運営と「在庫管理」の精度を大幅に向上させ、ミスの起こらない環境を実現するために極めて重要です。カスタマイズ可能なWMSは、個々のビジネスモデルや特有の運用要件に合わせて柔軟に設定を変更できるため、倉庫の効率性を最大化し、在庫管理の誤差を最小限に抑えることができます。
この種のWMSを導入する最大の利点は、倉庫内の特定の作業フローや在庫管理プロセスを細かく調整できる点にあります。例えば、商品のピッキングプロセス、在庫補充ルール、出荷検証プロセスなど、特定の業務に最適な設定を適用することが可能です。これにより、作業ミスが減少し、全体としての作業効率が向上します。
また、カスタマイズ性の高いWMSは、リアルタイムの在庫データと統合されることで、在庫レベルの精度を高め、在庫過剰や欠品のリスクを減少させます。さらに、自動化されたデータ収集と分析機能により、在庫管理の決定を支援し、より迅速で正確な意思決定を可能にします。
導入するWMSがビジネスニーズに適切に対応できるよう、事前の詳細な要件定義と、提供されるカスタマイズオプションの十分な検討が必要です。このアプローチにより、倉庫運営の効率化とコスト削減を実現し、顧客満足度を向上させることができます。
WMS導入による効率化とコスト削減
WMSの導入は、「倉庫」運営の効率化とコスト削減に直接的に寄与します。具体的には、WMSにより在庫管理プロセスが自動化されることで、手動でのデータ入力やエラーの発生が大幅に減少し、作業効率が向上します。また、WMSによる在庫レベルの最適化は、不必要な在庫の保持コストを削減し、倉庫内のスペースをより効果的に使用することを可能にします。さらに、出荷プロセスの高速化と精度の向上は、顧客からの信頼獲得につながり、結果的に収益性の向上を実現します。WMSは、「倉庫」運営と「在庫管理」のあらゆる面でコスト削減と効率化を促進するための強力なツールです。
ヒューマンエラーの削減
ヒューマンエラーの削減は、「倉庫」運営と「在庫管理」において、作業効率を向上させ、コストを削減する上で重要な要素です。人的ミスを減らすことは、プロセスの正確性を高め、顧客満足度を保持するために不可欠です。
エラー発生の主な理由
「倉庫」内でのヒューマンエラー発生の主な理由には、不十分なトレーニング、作業プロセスの複雑さ、過剰な作業負荷、適切なツールやシステムの欠如が挙げられます。これらは全て、「在庫管理」の精度を損ない、作業効率を低下させる要因となります。効果的な在庫管理と倉庫運営を実現するためには、これらの原因を特定し、具体的な対策を講じる必要があります。
トレーニングと教育の強化
トレーニングと教育の強化は、ヒューマンエラーを削減する上で最も効果的な方法の一つです。「倉庫」作業員に対する定期的なトレーニングプログラムを実施することで、「在庫管理」に関する知識を深め、作業手順を正確に理解させることができます。また、新しい技術やシステムの使用方法についての教育を行うことで、作業の効率化とエラーの削減を実現します。トレーニングと教育は、作業員の能力向上とモチベーションの維持にも繋がります。
プロセスの標準化と自動化
プロセスの標準化は、作業手順を明確にし、一貫性を保つことでヒューマンエラーを減らす効果的な手法です。明確な作業基準を設定することで、「倉庫」内の作業員が正しい手順で作業を行えるようになり、「在庫管理」の精度も向上します。さらに、在庫管理プロセスの自動化を進めることで、手作業によるエラーを大幅に削減できます。自動化されたシステムは、在庫の追跡、データ入力、在庫補充などの作業を正確かつ迅速に実行し、人的ミスを防ぎます。プロセスの標準化と自動化は、倉庫運営の効率化とコスト削減に貢献する重要な戦略です。
作業プロセスの見直しと改善
作業プロセスの見直しと改善は、「倉庫」運営と「在庫管理」の効率を向上させるために不可欠です。特に、物流センターのレイアウト最適化やピッキング・パッキングプロセスの効率化は、作業時間の短縮、コスト削減、顧客満足度の向上に直結します。
レイアウトの最適化
「倉庫」のレイアウトを最適化することで、作業効率が大幅に改善されます。この最適化には、在庫品目の配置再考、頻繁に動かされる商品のアクセス容易性の向上、受け入れ・出荷エリアの流れの改善などが含まれます。レイアウト最適化の目的は、物品の移動距離を短縮し、ピッキングや梱包の時間を減らすことにあります。また、安全性の向上や在庫の精度を高めるためにも、物理的な空間の配置を効果的に行う必要があります。「倉庫」内の空間を効率的に利用することで、「在庫管理」の精度も向上し、全体の運営効率が向上します。
ピッキングとパッキングプロセスの効率化
ピッキングとパッキングプロセスの効率化は、倉庫内作業の中でも特に重要な要素です。これらのプロセスを改善するためには、正確な在庫データに基づいたピッキングリストの生成、ピッキング経路の最適化、マルチオーダーピッキングの導入などが効果的です。また、パッキングプロセスにおいては、梱包資材の事前準備や自動化機器の導入により、作業の速度と正確性を向上させることができます。ピッキングとパッキングの効率化は、出荷エラーの削減に繋がり、顧客からの信頼獲得と再購入率の向上に寄与します。効率的なプロセスにより、倉庫運営コストの削減と「在庫管理」の精度向上を実現できます。
コスト削減以外のメリット
「倉庫」運営と「在庫管理」の効率化によって得られるメリットは、コスト削減だけに留まりません。これらの改善は、顧客満足度の向上やリードタイムの短縮にも大きく貢献し、企業の競争力を高める重要な要素となります。
顧客満足度の向上
効率的な「倉庫」運営と「在庫管理」は、顧客満足度の向上に直接的に寄与します。在庫情報の正確性が保たれることで、顧客への正確な納期情報の提供が可能となり、注文から配送までのプロセスがスムーズに進行します。また、ピッキングミスの減少は誤配送を防ぎ、顧客が正しい商品を期待通りに受け取ることができるため、顧客の信頼と満足度が向上します。顧客体験の向上は、リピート購入や口コミによる新規顧客の獲得に繋がります。
リードタイムの短縮
「倉庫」の効率化と「在庫管理」の最適化は、リードタイムの短縮にも貢献します。在庫の迅速な回転と出荷プロセスの高速化により、顧客の手元に商品が届くまでの時間が大幅に短縮されます。これは、特に迅速な配送を重視するeコマース業界において、企業が競争上の優位性を確立する上で重要な要素です。リードタイムの短縮は、顧客満足度の向上に直結し、市場でのブランドイメージの強化にも寄与します。効果的な在庫管理と倉庫運営により、顧客に対して迅速で信頼性の高いサービスを提供することが可能となります。
継続的な改善と評価
「倉庫」運営と「在庫管理」プロセスの効率化は、一度の取り組みで完了するものではありません。継続的な改善と評価を行うことで、業務の効率を最大化し、長期的な成果を確保することが可能です。
定期的なレビューとフィードバックの仕組み
倉庫運営と在庫管理のプロセスを最適化するためには、定期的なレビューとフィードバックの仕組みが不可欠です。このプロセスには、作業員や管理者からのフィードバックの収集、データ分析に基づくパフォーマンスの評価、および外部の専門家による監査が含まれます。定期的にこれらの活動を行うことで、「倉庫」内の作業効率や「在庫管理」の精度に問題がないかを確認し、必要に応じて改善策を講じることができます。効果的なフィードバックシステムを構築することは、持続可能な成長への道を開く鍵となります。
改善策の実施と効果測定
改善策を実施した後は、その効果を正確に測定し、評価することが重要です。これには、具体的な指標を設定し、前後比較を行うことが含まれます。例えば、ピッキング時間の短縮、在庫精度の向上、顧客満足度の改善など、定量的なデータを用いて改善の効果を測定します。効果測定を通じて、実施した改善策が期待した成果を生んでいるかを評価し、さらなる改善点がないかを検討します。継続的な改善と効果測定は、「倉庫」運営と「在庫管理」のプロセスを常に最適な状態に保つために不可欠です。
まとめ
倉庫運営と在庫管理においては、継続的な改善と評価が成功の鍵を握ります。定期的なレビューとフィードバックの仕組みを確立し、実施した改善策の効果を正確に測定することで、プロセスの効率化を図り、業務の質を向上させることができます。このような継続的な取り組みにより、倉庫運営と在庫管理の最適化を実現し、長期的な競争力を確保することが可能になります。