【倉庫管理者向け】誤出荷の原因と対策方法の解説
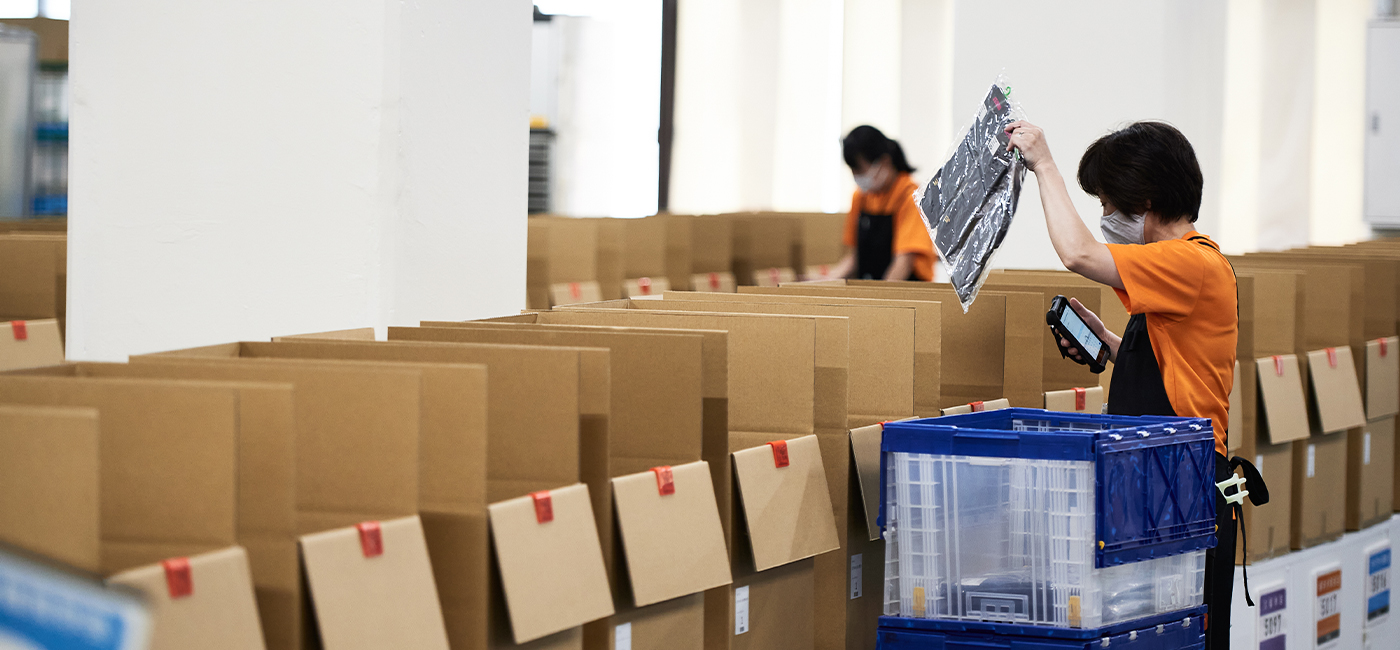
物流では、ピッキング時や出荷検品作業を行う際にミスが発生すると、数量や送付先を間違えて出荷する「誤出荷」に繋がります。特に倉庫作業では、WMS(倉庫管理システム)やマテハン機器導入が進んだ現在でも人的作業(納品書の封入、送り状の貼り付け、WMSを手動で操作することによるロットナンバーや賞味期限(消費期限)の登録など)が多く、ヒューマンエラーが起きやすい環境にあります。
そこで今回の記事では、倉庫作業における誤出荷の原因と、その対策方法について解説します。
【誤出荷のパターンと原因】
誤出荷にはさまざまなパターンが存在し、起こる原因も多種多様です。ここでは、その中でも特に代表的なミスの例について確認していきます。
①数量ミス
まず、誤出荷の中で最も発生頻度が高いのが数量ミスです。数量ミスの原因は、大きく分けて“ピッキング時の作業ミス”と“数量認識のミス”の2種類です。
ピッキング時の作業ミスの場合、「商品を1点取ったつもりが、商品が重なっており気づかず2点取っていた」というエラーです。数量認識のミスの場合は、「指示書の読み間違いで2ピースと記載されているところを1ピースだと思い込んでいた」というケースです。特にEC物流の場合、ほとんどの場合1ピースで購入されることが多いため、稀に2ピースの注文が入った際に作業者が無意識に1ピースしかピッキングをしないという誤出荷は起こりやすいと言えます。
「出荷検品時にバーコードのスキャンを行えば誤出荷はゼロにできる」と思われがちですが、“2度鳴き“や“鳴き漏れ“があるため数量ミスをゼロにするということは決して簡単ではありません。特にBtoB物流であれば、1件の出荷ピースが数百ピースということもあるため、正しく全数をスキャンするための手順やルールを構築し、例外なく実行させる必要があります。
また、ケース出荷とバラ出荷のバーコードが同じ(正梱ケースに貼られているバーコードと商品単品に貼られているバーコードが同じ)ケースにおいて、出荷数が“3”と記載されている場合、3ケースとバラ3つのピッキングを間違えたとしてもJANコードが全く同じなため、出荷検品でも誤出荷を止められないということもありえます。
さらに、後述のとおりロットナンバーや賞味期限(消費期限)が異なるだけの同じアイテムの商品バーコードが同じであれば、単にスキャンすることで間違いのないロットや賞味期限(消費期限)の商品を出すということは実現できません。
②送り状の貼り間違い・納品書の入れ間違い
誤出荷のパターンとして数量ミスに並んで多いのが、伝票に関するヒューマンエラーです。出荷商品の宛先を間違えることで、相手に予定とは異なる商品が届くだけでなく、個人情報の流出にも繋がりかねません。複数の送り先がある状態で、送り状ラベルをテレコで貼ってしまうことで発生するケースが多いと言えます。
送り先が間違っている場合、その商品が全て間違っていることになるため影響度は甚大です。間違っている商品も別の顧客向けの商材であるため、スピーディーに返送してもらいたいところですが、発送側の不手際であるため交渉しづらいというのが実態です。したがって、2つの送り先に正しい商材をもう一度発送し、その後に誤出荷した商品を返送してもらい、正しく棚入れを行う必要があります。
また、同梱する納品書の入れ間違いも少なくありません。1日で数百件以上の出荷対応を行うテレビ通販やネットショップであれば、納品書の数も膨大になるため入れ間違いのリスクも高まります。BtoCの場合は、倉庫管理システムを用いて伝票と商品の照合作業をデジタルで制御しやすいという側面もあります。一方でBtoB向けの場合、宛先の数は少ないものの、“チェーンストア統一伝票”や“百貨店統一伝票”などの専用伝票を使用することが多く、伝票と商品の照合作業を倉庫管理システムで制御するには物流に精通したSEがシステムをカスタマイズする必要があります。
伝票の入れ間違いについて、送ったアイテムは一致しているため影響は限定的と思われるかもしれませんがそんなことはありません。個人情報(住所、氏名、電話番号など)の漏洩は一般ユーザーであれば大きな不信感や不安感を抱きます。また、相手が企業であっても同様です。たとえば。卸先や販売先への伝票を入れ間違ってしまい、「特定の販売先に値段を優遇していること」や「熾烈な競合先同士に商品を出していること」などが判明した場合、卸先との関係性が悪化してしまうことも容易に考えられます。
③出荷商品(品番)の間違い
出荷商品(品番)の誤出荷とは、言葉のとおり出荷する商品を間違ってしまうことです。サイズ違いなどの“商品の見た目が非常に似ているケース”やシリーズ違いなどの“品番や品名の一部だけが異なる場合”に発生しやすくなります。ピッキング担当が間違うケースに加え、入庫時の段階で間違ったロケーションに保管してしまい、それを気づかずそのまま出荷してしまうパターンもあります。
すなわち、“ピッキングする人間”と“チェックする人間”で見間違える可能性が非常に高い相関をもってしまうため、ダブルチェックに意味がなくなってしまいます。
また、出荷アイテムの種類が多い時にピッキングリストに記載している行を飛ばしてしまい、商品が一部入っていないケースもあります。出荷数が限定的なEC販売などでは少ないかもしれませんが、卸先や自社店舗向けへの出荷では1回に数百アイテム、数千ピースということも珍しくないため、一部商品が漏れてしまうリスクは飛躍的に高まります。
生鮮食品やコスメなどを扱う場合は、賞味期限(消費期限)の管理にも注意が必要です。商品自体は間違っていなくても、「最低6か月以上期限が残っているものを届ける」「同一商品において、一度の入荷で異なる期限のものを混ぜない」など、事前の取り決めと異なるアイテムを誤って出荷してしまえば、トラブルに繋がってしまいます。
全商品の引き取りに加え、最悪の場合には取引停止という可能性もあります。懸命に商品を企画・開発し、営業部門がやっとの思いで百貨店、GMS、ショッピングセンターへの販路を開拓したにも関わらず、このような誤出荷によって取引停止となれば目も当てられません。
一方で、正確な期限管理を注意力に依存したアナログ作業で行うことは至難のワザです。外観は全く同じ商品であるため、「賞味期限(消費期限)の短いものから出荷する」「入荷した順番に先入先出で出荷する」を人の手で完璧に対応しようとすれば、保管スペースを物理的に分けて管理するなど余計なルールやコストが発生します。したがって、そのような期限に関する情報を物流システムで正確に制御し、コストを抑えた運用を行うことが不可欠です。
④紛失
ここでいう紛失とは、「帳簿ではあと1個残っているはずの商品が実際には無かった」という状況を想定しています。データでは在庫が1つあるため出荷引き当てが掛かり、ピッキング作業者が保管場所にいったところ商品が見つからないというケースです。この場合は“未出荷”になりますが、これも実質的には誤出荷です。
現代のユーザーは欠品となった商品が再入荷されるまでじっくり待ってはくれないでしょう。機能性やデザインで似た商材があればすぐに競合店で購入します。また、EC販売では注文完了後の欠品連絡となるため、エンドユーザーからの評価も厳しくなります。リピート客になったかもしれない新規顧客からの売り上げを逃しただけではなく、ネガティブな体験をしたという口コミ投稿者になってしまう可能性すらあるのです。
紛失による誤出荷の発生要因は様々ですが、よくあるケースとしては以下の通りです。
「入荷時の数を間違えて計上していた」
「過去の誤出荷によって、データと実物の数がズレている」
「商品を棚入れする際に、違うロケーションに入れてしまった」
「営業担当がサンプルとして持ち出したことが在庫データに反映されていない」
「不良品が混ざっており、取り除いたが在庫データに反映されていない」
このようなケースが続くと在庫差異がどんどん大きくなります。紛失は出荷時だけでなく、全ての作業工程(入荷時やスペース確保のためのロケーション変更中)でも発生する可能性があるため、入出荷履歴や在庫移動データをいつでも遡って確認できるようにしておくことは必要不可欠と言えます。
⑤出荷指示書の情報入力ミス
出荷指示書(ピッキングリスト)の情報入力によって起こるミスもあります。ピッキング作業をする際、どんなに作業が正確であっても、出荷指示書の内容が間違っていれば100%出荷ミスとなります。誤出荷を防ぐためには、現場作業員による注意も必要ですが、出荷指示書を作成する受注管理側もミスが無いように十分配慮することが大切です。
ただし、受注管理では非常に多くのイレギュラー対応が手管理で求められるため、入力ミスをゼロにする事は相当難しいといえます。たとえばEC販売ではエンドユーザーから多くのリクエストが寄せられます。
「10時の注文と12時の注文を同梱して欲しい」
「コンビニ後払い決済をしていたが、代引きに変更したい」
「購入した注文の一部だけサイズ変更orキャンセルしたい」
「届け日を変更したい」
「送り先を自宅ではなく、郵便局留めにしたい」
このような依頼事項は、一般的なパッケージ型の受注管理システムでは自動処理ができないため、ECモールの管理システム内でアナログ的に対応することになります。しかも決済手段や販売額の変更によって送料無料ラインを割ってしまうケースや手数料を手修正で変更することも多く、ミスに気付かない場合が少なくありません。
また、電話注文、FAX受注、不良対応などの場合に受注処理そのものを手管理で作成する場合も多くの手入力項目が発生するため、ヒューマンエラーは発生しやすいといえます。しかも、あらかじめサイト内で決められた時間までの注文は当日出荷を約束していることが多いため、時間的な制約の中での緻密な作業が求められます。特に「Qoo10メガ割り」「楽天スーパーSALE」「超PayPay祭」などの大型セール時にミスが増加することが多いでしょう。
打開策としては、物流システム側でデータ変換処理ツールを構築するなど、システム連携をベースとした生産性の高い受注管理を行うことでアナログ領域であってもチェック機能をシステム化できるため、ミスを大幅に削減することができます。
⑥ロット指定のミス
食品や医療機器などの現場で起こりやすいのが、ロットに関連した誤出荷です。特に賞味期限(消費期限)は最終ロットの確認を個別に行って、前回より新しいロットが出荷される必要があります。そのため、ロット指定が逆転しないように注意をすることが求められます。
ロット指定の誤出荷が起きると、その食品や医療機器は使用することができなかったり、使用することで人体に悪影響が出る可能性が考えられます。そのような事態は、販売先の信頼を大きく棄損することに繋がるため、細心の注意を払って避ける必要があります。
また、販売先によって、ロットの逆転に加えてロットが跨ってしまうことも許されないことがあります。仮に注文数に対してロットの跨りを防ぐために次のロットの商材を出荷した場合、前のロットの商品がいくら余っていてもその販売先には出荷できなくなってしまいます。この問題を防ぐには、各商品のロットごとの残数を勘案し、“売れ残りを最小にするロットと販売先の最適な組み合わせ”を計算するアルゴリズムがWMSに組み込まれていることが必要となります。
その他にも、医療機器における細やかなロット管理として、滅菌期限等の管理や使用回数のトレーサビリティなども必要ですが、アナログで対応することは至難の業ですし確実にヒューマンエラーが発生するでしょう。このような細かい条件設定も業務に合わせてカスタマイズされたWMSであれば組み込むことが可能ですし、生産管理システムや受注管理システムなどの他システムとの連携もスムーズになるため、人事的なミスが生じる隙がありません。
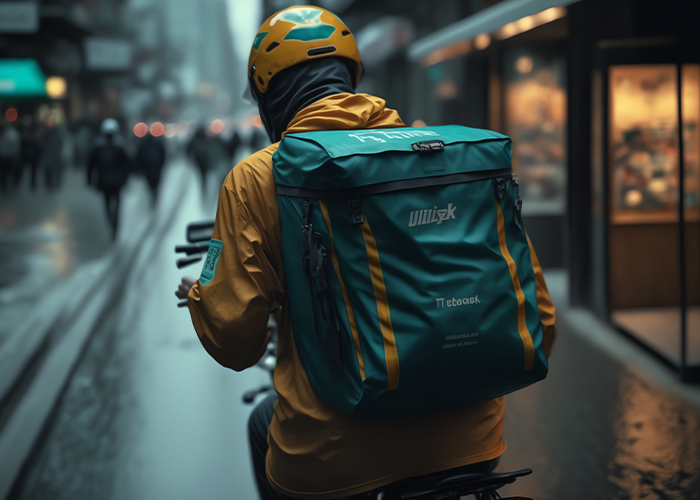
⑦配送日時・指定時間の間違い
配送日時を間違えてしまうこともエンドユーザーからすれば誤出荷になります。その日に届けるという顧客との約束を破ってしまっているからです。“母の日ギフト”“誕生日プレゼント”“クリスマスギフト”など、特別な届け物で日時指定が守られなかった場合、購入者は相当ガッカリしてしまうでしょう。
BtoCの運送の場合、ヤマト運輸や佐川急便などに委託するしかなく、倉庫管理側で出来ることは限定的と思われるかもしれませんが、そんなことはありません。倉庫管理側で例えばエリアごとに商品を運びやすい状況で集荷時に予め準備をしておくことで、運送会社がエリアごとに仕分ける手間や、数量を数える手間を圧倒的に減らす事が可能になります。
そうすることで、(1)運送会社が集荷後にエリアの仕分けを間違えたり(2)個数を間違って数えたり(3)口割れを起こすリスクが減少します。また、ドライバーの待ち時間やトラックに運び込む時間の圧縮にも繋がるため、ドライバーが予定通りに配送することに繋がります。
また、配送中の商品破損ということもあります。待ちに待った商品を開梱したところ、中身が破損していたら購入者はどう感じるでしょうか?商品が正しい状態で届いて初めて正しく出荷されたと言えるでしょう。
ドライバーの運転に依存することもありますが、倉庫管理側で出来ることとしては丁寧に梱包することにつきます。緩衝材を上手く活用するとともに、商品の特性に応じた丁寧な梱包が大切です。また重複にはなりますが、倉庫管理側で商品を整理整頓し、すぐにトラックに積める状況を作っておくことにより、ドライバーの肉体的・精神的負担をできるかぎり減らすことにより、ドライバーが自然と安全運転となるような状況を作ることも期待できます。
【誤出荷が起きると問題なワケ】
誤出荷は、ただ商品内容を取り違えるだけの単純なミスではありません。それを原因として、管理の問題や信頼に対する問題に繋がる危険性を孕んでいます。ここでは、3つの具体例を紹介します。
①エンドユーザーや販売先からの信頼がなくなり、売上や利益が下がる
商品間違いや数量ミスなどは、一度でも起こせば相手からの信頼を失ってしまい、将来的に多くの機会損失に繋がります。顧客は注文したら正しく商品が届くことを前提に待っているため、一度でもミスがあれば、一気に信頼を失い、二度と注文をしてくれなくなることも少なくありません。作業をする側にとっては「たった1回」でも、顧客側からすれば大切な1回です。大切な家族や恩人へのプレゼントで誤出荷が発生した場合、注文した方と送られた方の双方の信頼が失墜することでしょう。
誤出荷はエンドユーザーだけでなく、大切な販売先(百貨店、ショッピングセンター、楽天・AmazonなどのECモール)を失うことにも直結します。弊社のお客様でも、弊社との取引前に百貨店やショッピングセンターにおいて、「これ以上出荷精度が悪化するようであれば、販売を停止する」という警告を受けた荷主様もいらっしゃいます。
EC通販の場合、モールからの撤退は死活問題ですが、そこまでいかなくとも誤出荷・欠品・出荷遅延など物流品質が悪化した場合、「モール内の露出度が下がる」「特定の商品を販売することが出来なくなる」などのペナルティが与えられます。近年はコロナウイルスの影響もありEC販売の取扱量は増加しており、特に季節ごとのイベントや四半期セールの集客力には目を見張るものがあります。誤出荷が続けば将来的に得られたであろう多くの売上がなくなってしまう可能性を孕んでいます。

②在庫差異は“販売活動へのマイナス”と“無駄なコスト”をもたらす
数量ミスや商品の取り違えによって生じる誤出荷は、在庫管理に影響を与えます。誤出荷に気づかず在庫管理を続けていると、データ上の在庫と実在庫の間にズレが生まれ、「データ上はないことになっているため、倉庫内で商品が埃をかぶって売れ残り続ける」「データ上はあることになっているものの、実際は存在しないため受注後に必要な在庫数が確保できず欠品になる」などの問題が起こります。これらの在庫差異は効果的な販売施策を実現させるためには大きな障壁となります。
また、在庫差異は無駄な管理コストを膨らませることにも繋がります。特に品番間違いによる出荷ミスの場合、正しい商品へ交換する作業料や発送料に加え、間違った商品を返送するための返送料、返品された商品を販売可能な状態に戻すためのリバイバル作業に掛かる人件費などが発生します。また、誤出荷が及ぼす問題はこのような直接的なコストだけではありません。1つの誤出荷は2アイテムの在庫差異を発生させる要因になります。本来送るべきだった商品をA、誤って送った商品Bをしましょう。1件の誤出荷から適正な在庫状態へ戻すには、以下のフローが必要です。①間違って送ってしまった商品Bを在庫管理システムで手補正(マイナス1)する②本来送るべきだったAをお客様へ発送する(ただし、この出荷は通常の注文でないため、受注管理システムから生成されたものではなく、手入力で作る必要がある)③誤って発送した商品Bの返品をお客様に依頼し、返品されたらその時点でその商品を検品し問題がなければ入庫する(ただし、いつ返品されるか分からない)④在庫管理システムでBを1個手補正する(プラス1)
このように、たった1件の誤出荷で生じた在庫差異を完全に戻すには上記の4フローを全てアナログで実行する必要があります。入力を間違えるリスクに加え、商品Aの返品については①卸先の場合は1か月後に何かのついでに他の商材と纏めて送られてくる②一般ユーザーの場合は「連絡が取れずに返してもらえない」「タグやシール等が取れてしまってAと判別できない」ということもあり得ます。毎日膨大な商品が通過している物流センターの中で、まだ返品されていない商品数をリアルタイムで把握し、日々の入庫との突合せを実施しつづけることは途方もない手間です。
このように、たった1件の誤出荷でさえ、直接的な作業コストに加えてそのあと在庫差異が完全になくなった状態に戻すための手間が掛かることは理解いただけたかと思います。誤出荷が数件単位で出てしまったらもう在庫差異をゼロにすることは至難の業です。つまり在庫差異を出さずに精緻な在庫管理をするには誤出荷ゼロを徹底するしかありません。
③従業員が大きく疲弊する
誤出荷の頻度が高まると、従業員の負担は確実に増加します。
前述のとおり、大型のセールイベントなど出荷数が多くなった時ほど出荷ミスの比率は増加します。間違った商品の返品・交換に関する手続きは返金や金額変更などの金銭に関連するアナログ処理であり、1つのミスが大きな2次クレームを引き起こす可能性があるため、正確かつ慎重な対応が求められます。したがって、誤出荷の件数が増えるほど、注文処理を担当している従業員の心理的ストレスは増加します。
疲弊するのは受注担当だけではありません。企業間の出荷ミスの場合、営業担当者は謝罪に加えて原因の究明と再発防止策の説明、代わりの商材手配など、本来する必要のなかった営業活動以外の業務に奔走することとなります。今後の取引関係にも大きな影響を及ぼすことが予想されるため、その精神的ストレスは大きなものとなります。
それでも企業間取引の場合、積み上げてきた信頼関係を活かしながら適切なタイミングで迅速かつ丁寧に対応することでクレームを和らげることは可能でしょう。しかしながら、相手が一般のエンドユーザーの場合、しばしば心無いクレームや脅迫めいた過度な要求に発展することもあります。そのブランドが好きで、懸命に働いている従業員がそのようなクレームが原因でモチベーションが下がり、離職してしまえばその影響は甚大と言えます
また前述のとおり、誤出荷が発生することで、「アナログでの出荷作業が必要となり、目検での確認作業を都度おこなう」「入荷予定のない返品物を日々チェックし、棚入れする」など、物流スタッフのイレギュラー対応が増えることになるため、現場は確実に疲弊します。さらに出荷が頻発している場合、在庫差異が常態化していることが予想されます。
在庫差異が常態化することで、毎日のように「商品があるべきロケーションで見つからない」ということが発生し、物流スタッフの心理的疲弊は相当のものと推測されます。これでは作業者のモチベーションも作業の生産性も上がるわけがありません。この悪循環がさらに連鎖していくと、作業者自身の不注意や錯誤で行くべきロケーションを誤っていた場合にも「商品がまた定位置にない」と、正しいロケーションに置かれている商材をわざわざ広い倉庫の中で無駄に探しまわるという本末転倒な事態にさえ陥ります。
【誤出荷ゼロを達成するための具体的な方法】
ここは三協がどのようにして誤出荷ゼロを実現しているかについて具体的にお話します。
誤出荷を防ぐためには、日々対策を行う必要があります。ここでは、対策を行ううえで重要な点を3つ説明します。
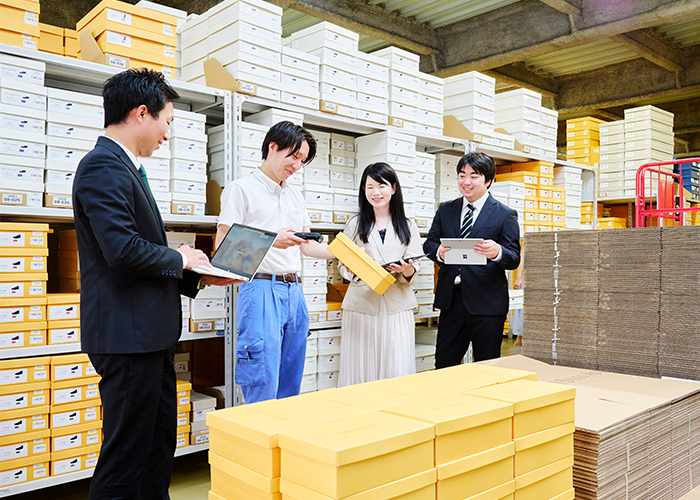
①対策するにはまず原因を特定する
対策を立てるには、まずは原因を知る必要があります。一括りに誤出荷と言っても、その原因はケースごとに異なります。そのため、「なぜその誤出荷が起きたのか」が具体的にわからなければ、適切な対策を取ることはできません。基幹システムを中心とするシステムの構築環境・人員のヒューマンエラー・部門間の情報連携・機材のエラー・ロケーション管理の問題など、まずは大まかな分類から入り、ひとつひとつの段階を追っていって、確実に原因を抑えるようにしましょう。
誤出荷の根本原因を特定するうえで、最も難しいのは複合的な要因が合わさってできているということです。誤出荷は、製造部門、調達部門、販売部門、システム部門など各セクションの影響を受けたために発生するため、物流部門が単独で解決することはほぼ不可能です。したがって、まずは部門横断的に情報を集約・整理し、実際に起こっている問題箇所を突き止める必要があります。
次に、誤出荷の原因が「業務ルールに無理があるケース」と「業務ルールが守られていないケース」とのどちらであるかを判別する必要があります。業務ルールに問題があるケースとは、①非常に紛らわしい品番を目視でチェックし出荷する②納品先毎に異なるルールに基づいて梱包や同梱物を入れるといったケースです。このような場合、“高い集中力”や“複数の納品ルールを覚えるための物流経験や記憶力”が必要となるなど、その業務ルールを守りたくても能力や経験不足で守ることが出来ないために、誤出荷が発生してしまうということは少なくありません。
私たちは「誤出荷が止まらない」というお悩みを、1年に100件以上お聞きしますが、その大部分は「業務ルールに無理があるケース」です。問題なのは、その事実を無視しスタッフの注意力が散漫であるという誤った結論で物流スタッフのケアレスミスであると片づけられてしまうことが多いということです。
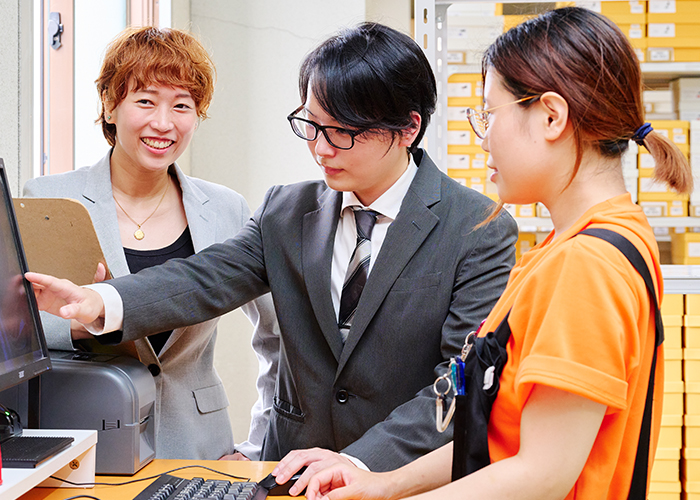
②誤出荷が発生しない“仕組み”を構築する
コンビニを想像してください。複雑なことを簡単なオペレーションで実現可能にしています。お弁当の賞味期限管理、チケットの予約、在庫管理、公共料金の引き落とし、多数の決済手段など、様々なことが出来て便利ですが、店員さんは涼しい顔でオペレーションをこなしています。老若男女、国籍を問わず、高品質なサービスを実現しています。それは、よくできた仕組みが出来ているからです。
物流に置き換えるとどうなるでしょう。三協では、部門横断的に情報を集めたうえで誤出荷を一切出さないための物流フローを人間工学、安全工学に基づいて科学的に構築しています。究極的には「誤出荷を出したくてもだせない」というレベルまで物流フローを細部まで作り込むことが大切です。
たとえば、納品先ごとに異なる同梱物やセット商材を入れる必要があるケースを考えます。
通常であれば、作業者が記憶やマニュアルをチェックしながら作業するということが多いですが、これは必ず誤出荷が発生します。人によって記憶力に差がありますし、思い込みや記憶違いでヒューマンエラーが発生することでしょう。しかも、こういった作業ルールは納品先の変更や追加などで頻繁に変わるため、そのたびにマニュアルをアップデートさせ続ける必要があります。その結果、熟練スタッフしかその作業が出来ないという業務の属人化・専任化ができあがってしまい、「特定のスタッフだけが休みを取れない」⇒「常に多忙なため、他の作業者に仕事を引き継げない」⇒「熟練スタッフだけで作業を行うため、マニュアルも更新されない」⇒「誤出荷が出ても他に作業ができるスタッフが限られるため、強く言えず抜本的な改善ができない」といった負のスパイラルに陥ってしまい、気づいたときには誤出荷を改善することはかなり難しくなってしまいます。
では具体的にどうやって誤出荷を引き起こさない仕組みを構築するのでしょうか。先ほどの納品先ごとに異なる同梱物やセット商材を入れる必要があるケースで考えます。三協であれば物流システムの“納品先マスタ”や“セット品マスタ”を徹底的に整備し、システムの画面で必要な同梱物やセット品が画面上で分かりやすくポップアップされるようにカスタマイズをおこないます。こうすることで、入社その日のアルバイトスタッフであっても、デジタル上で指示されたとおりに画面を操作すれば間違えずに作業を出来るようになります。
ここで大切なことは曖昧さを排除し、100人が100人とも考えなくても自然にルール通りに作業できる仕組みを構築することです。そのためには重要な要素が2つあります。1つは、誤出荷をゼロにするための物流フロー(扱う商材に適したロケーション管理、マテハン機器の選定、仕入戦略や販売施策にマッチした入出荷方法、販売管理システムや受注管理システムからのデータ連携など)を構築すること、2つ目はその物流フローを具現化するための倉庫管理システム(WMS)を開発することです。システム開発には、タグやボタンの配置・フォントの大きさ・配色・読み取り音の種類など、画面設計や操作性にとことんこだわることが必要であるため、物流に精通したエンジニアの存在が不可欠と言えます。三協のSEはシステム会社のエンジニアではないため、WMSに特化しています。また、現場に何度も足を運び、使いやすさを聞き、日々改善を繰り返しているからこそ、作業者が心から使いやすいと思うWMSを構築できているといえます。
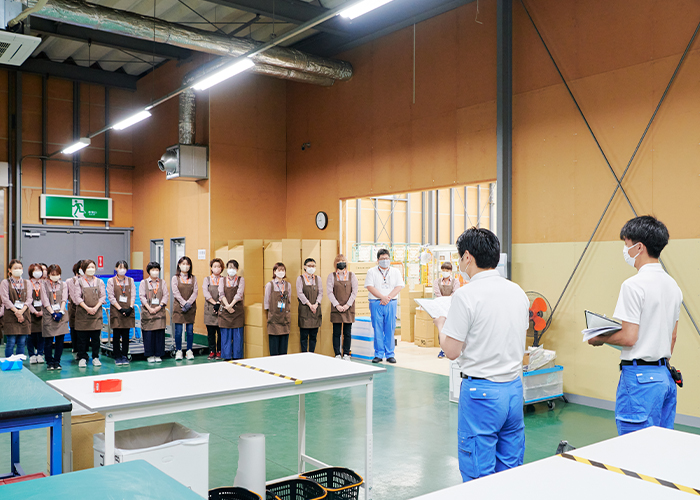
③仕組みが正しく機能するための“しつけ”を浸透させる
誤出荷をゼロにするには、前述のとおり仕組みが大切ですが同様に「誤出荷をゼロにしなければいけない」という意識が全てのスタッフの中で醸成されていることが不可欠です。
三協では、300人以上のスタッフ(アルバイトさんパートさんを含めて)が合計9拠点で働いていますが、「三協で一番大事なことは何ですか?」と尋ねられれば、誰にいつ聞いたとしても、たった一人の例外もなく「誤出荷を出さないことです。」と間違いなく返答します。それくらい、三協では誤出荷ゼロにこだわり、社内に浸透させています。
「誤出荷を決して出さない」という意識をスタッフが持つ環境作りも大切です。5S(整理、整頓、清潔、清掃、しつけ)の徹底のような基本的なことはもちろん、三協には“真っ直ぐにする”という哲学が存在します。真っ直ぐとはパレットや段ボールの位置をただ揃えることではなく、躾や心構えを指す言葉です。常に真っ直ぐな状態だからこそ、ちょっとした違和感や小さなアラームを見逃すことなく業務を遂行することが出来ます。少し位の歪みなら品質に問題ない、と思う従業員が一人でも居れば、状態は悪化していき、行き着く先は乱雑な倉庫となるでしょう。
すなわち誤出荷ゼロは、仕組みに加え、「絶対に誤出荷を出してはならない」という執念にも似た意識統一の上で成り立っています。
【三協の誤出荷レベルについて】
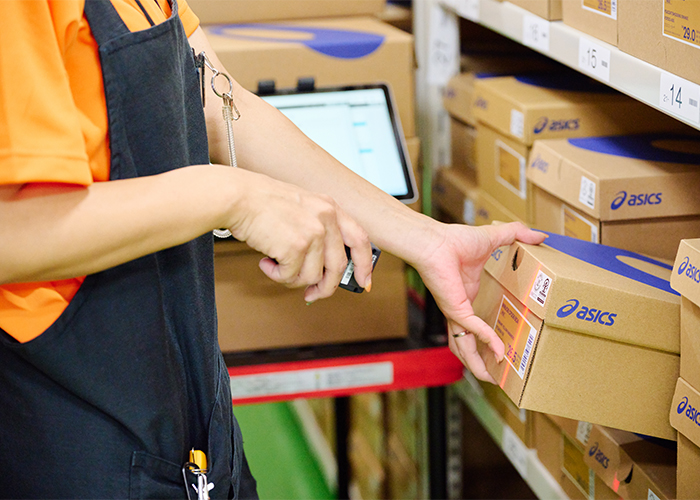
2022年末時点において、三協の物流アウトソーシングにおける数値は0.37PPMとなっております。すなわち270万件に1件(0.00004%)以下の誤出荷率を物流代行において実現しています。なお、270万件に1件の誤出荷には入出荷に関するマスタや取引データを頂戴できず、弊社のWMSを一切使用することができないお客様が含まれております。したがって、弊社が開発している物流システムを使っているその他のお客様についての出荷精度はさらに高い結果となっております。
手前みそではありますが、90社のほぼ全てのお客様において、取引を開始してからこれまで誤出荷を発生させたことはありません。三協に物流アウトソーシングをした結果、誤出荷が出ないため、棚卸や販売店側での確認作業を無くしたというお客様もいらっしゃいます。また、三協は近隣に住んでいるパートスタッフ中心で業務を遂行しているため、コストを抑えたうえで世界最高峰の物流精度を実現しています。
【最新のマテハンで誤出荷ゼロは達成できるのか】
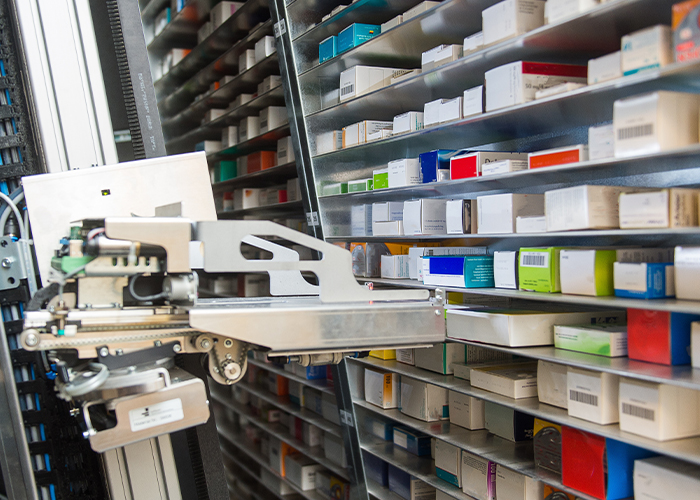
「自動倉庫や物流ロボットなどの最新のマテハン機器を導入すれば誤出荷は止まりますか?」という質問をされることがよくあります。この問いに対する答えとしては、ケースバイケースというのが私たちの答えになります。
もし、商品の形状やSKU数が限られているペットボトル飲料水などであれば有効に機能します。一方で、自動倉庫や物流ロボットはベースとしてはパッケージとして作られており、事業者様の業種や業態、販売方法や作業手順を考慮して作られているわけではありません。
すなわち、自動倉庫や物流ロボットなどの先進的なマテハン機器は、企業ごとの業務に合わせて作られておらず、多くの場合その隙間を作業者である人間が埋めることになります。
「この納入先については、特別の納入方法なので自動化の対象外のため、人が例外的にピッキングをする」
「一部商材は棚入れをさせずにそのまま即出荷させるので手管理になる」
このように販売戦略や仕入戦略が多様化・複雑化するにつれ、生き物のように変化するのが物流であり、そのすべてをマテハン機器だけで自動的に対応するというのは難しいことが多いというのが率直な我々の感想です。
もし、それらを完全にマテハン機器だけで対応させようとした場合、メーカーとの交渉時間や多額のメンテナンス費用が発生することとなります。また、仮に経営方針が変わり、マテハン機器が不要になった場合、多額の損失が発生するリスクも考慮する必要があります。
マテハン機器のうち、ソーターやGASなどはシステムエンジニアの力を用いることで、ほぼ同じ効果を疑似的に生成することも可能です。プログラムであれば仮にそれが不要になった際には処分ということに頭を悩ませることもなく、変化に強い戦略を構築することが可能です。
最も大切な事は、①定型化しており機械を入れた方が良いこと②不確実性が高く、カスタマイズ可能なシステムで管理すること③人間が柔軟に対応したほうが良いことの配分を戦略的に考えて将来を見据えた物流管理を行うことではないでしょうか。
【まとめ】誤出荷をゼロにして利益を最大化しよう!
今回は、誤出荷の原因や対策、問題の本質などについて取り上げました。誤出荷を防ぐためには、ミスをなくすよう現場の作業員に指導をするだけでは絶対に達成できません。全社的に正しく原因を知り、システムを巻き込んでの最適な物流フローを構築する必要があります。誤出荷がゼロになり物流が円滑にまわれば、余分な保管コストや作業コストが減るだけでなく、機動的な販売施策や仕入施策が実現できるため、売上の最大化を実現することも可能になります。働く人のモチベーションアップにも繋がりますのでぜひ実現しましょう。